How to Supply Plan Long Lead Time vs Short Lead Time Items
Executive Summary
- Lead time has a definition and has different categories.
- Important topics are lead-time accuracy, effective lead time, static versus effective lead time, and long lead time versus short lead-time items.
Introduction
Lead times are always in the background but often overlooked in supply chain management. Even central concepts put forward by Lean or JIT proponents are frequently based upon (in part) a misunderstanding of lead times versus the replenishment trigger. Much of the focus on lead times is on shortening them rather than how supply planning systems manage lead times. Consultants often discuss lead times not because they can do anything to shorten them but because they have lead time projects to sell companies. You will learn the common lead time categories and the concept of adequate lead time versus standard lead time and observe our analysis of common (and commonly confusing) lead time topics.
What Are Lead Times?
Lead times are the time between locations within or from a supply network.
The term lead time often includes processing at the beginning or end of the main consuming component. For instance, a standard lead time definition will consist of the total supplier or customer lead times, including the transportation lead time.
Common Lead Time Categories
The following are standard lead times that we will define.
- Manufacturing Lead Time Definition
- Procurement Lead Time Definition
- Stock Transfer Lead Time Definition
- Transportation Lead Time Definition
- Goods Issue Lead Time Definition
- Goods Receipt Lead Time Definition
- Quality Inspection Lead Time Definition
- Setup Lead Time Definition
- Total Lead Time Definition
Lead Time #1: Manufacturing Lead Time Definition
The time from when the production order is created to when the finished good is available.
Lead Time #2: Procurement Lead Time Definition
The time from when the procurement order is placed to when it is received.
Lead Time #3: Stock Transfer Lead Time Definition
When an item is issued from one internal facility to when it is received into another internal facility. Identical to the procurement lead-time, except it covers internal shipments rather than receiving shipments from external sources.
Lead Time #4: Transportation Lead Time Definition
The time from when an item is shipped to when it is received.
Lead Time #5: Goods Issue Lead Time Definition
The time from when an item is released to when it is available (generally for production or shipment)
Lead Time #6: Goods Receipt Lead Time Definition
The time from when the item is received to when it becomes available as inventory.
Lead Time #7: Quality Inspection Lead Time Definition
The time from when an item is released to when it passes quality inspection.
Lead Time #8: Setup Lead Time Definition
A subcomponent of the overall manufacturing lead-time.
Lead Time #9: Total Lead Time Definition
It is not a standardized term, as there is no “total lead time” within a system. Instead, it is a conceptual term.
Typically, it is the entire time an order is placed until the item is delivered.
Notice that some are not referred to as “lead times.” For instance, one would ordinarily use the term “setup time” rather than “setup lead time.” However, the setup time is a lead time required to complete a task.
The Importance of Lead Time Accuracy
One of the major issues related to determining lot size is data quality and lead time accuracy. For a supply planning system to calculate accurate dates, the system must have lead times that reflect the operations’ reality. The problem is that lead times often differ pretty substantially from reality.
- It should be noted that there is often a lead time variance from suppliers.
- There can also often lead time variances in manufacturing and outbound transportation.
Interestingly, this is not an issue that is discussed within companies. But it should be because it is a much broader problem than generally understood. And while there is a universal interest in forecast accuracy, lead time accuracy is often overlooked.
What is Lead Time and the Lead Time Meaning
Lead time means the time required to complete a supply chain process to ultimately provide a product to a customer.
Standard lead times include:
- Supplier Lead Time
- Manufacturing Lead Time
- Purchasing Lead Time
- Shipping Lead Time
Additionally, there are lead times from the demand side. This includes:
- Customer Lead Time
- Order Lead Time
Customer lead time and order lead time are considered to be synonyms.
Therefore, when the question “What is lead time,” the answer depends on what is being discussed.
Many companies make very high profits by importing products manufactured in low-wage countries. These products mostly come by ship and have extended lead times. While many Lean consultants have preached about lowering lead times, outsourcing manufacturing to these low-wage countries has caused lead times to lengthen quite significantly. However, the profits are so high on these items from a financial perspective. It makes sense to accept the long lead times.
Long Lead Time Items and Short Lead Time Items
A product location database can be segmented by the length of the lead time. A long versus short lead time can change depending on the company.
For many US companies, the division between long and short lead time items is whether the product is sourced overseas (often in China) or domestically. The locally sourced products cost more but come with short lead times.
Extended lead-time items must be planned considerably differently than short lead-time items, and there is less margin for error. Extended lead time items must carry more safety stock than quick lead-time items to compensate for this.
How to Reduce Lead Time and The Feasibility of Lead Time Reduction
It is often proposed that one can reduce lead times and reduce the impact of lead times on supply chain planning. But really, what is the feasibility of lead time reduction? It turns out that there are usually a few options to reduce lead times. The lead time with the highest feasibility of lead time reduction is normally shipping lead time.
However, shipping lead time is also typically expensive to reduce. The supposed case studies that are often used to show the feasibility of lead time reduction tend to have little published detail about them and, therefore, are difficult to verify independently.
How to Calculate Lead Times
To properly understand lead times, viewing the subcomponents of lead times is beneficial to determine the overall lead time. We covered this topic in the article How to Best Calculate Lead Times.
The Definition of Effective Lead Time
Until now, we have covered lead times as entered in systems or static lead times. However, another type of lead time is essential to understand that changes depending upon the specific circumstance of demand and applied to the supply network. This is the concept of effective lead time.
Effective lead time is only modeled if the category of supply planning software called multi-echelon planning is used.
- Different demand levels lead to different circumstances and need to move to a higher echelon in the supply network.
- The most important thing to consider is that effective lead times change while lead times between locations do not change (in the short term).
For software to be considered multi-echelon, it must have the ability to reflect the changes in adequate lead time in its planning. This is combined with inventory optimization, which is a different mathematics set. It allows the software to position inventory in the right location properly. Select the correct quantity based on the demand, the current stocking position, and the service level.
It can also be described graphically, allowing the reader to understand what adequate lead time is intuitive.
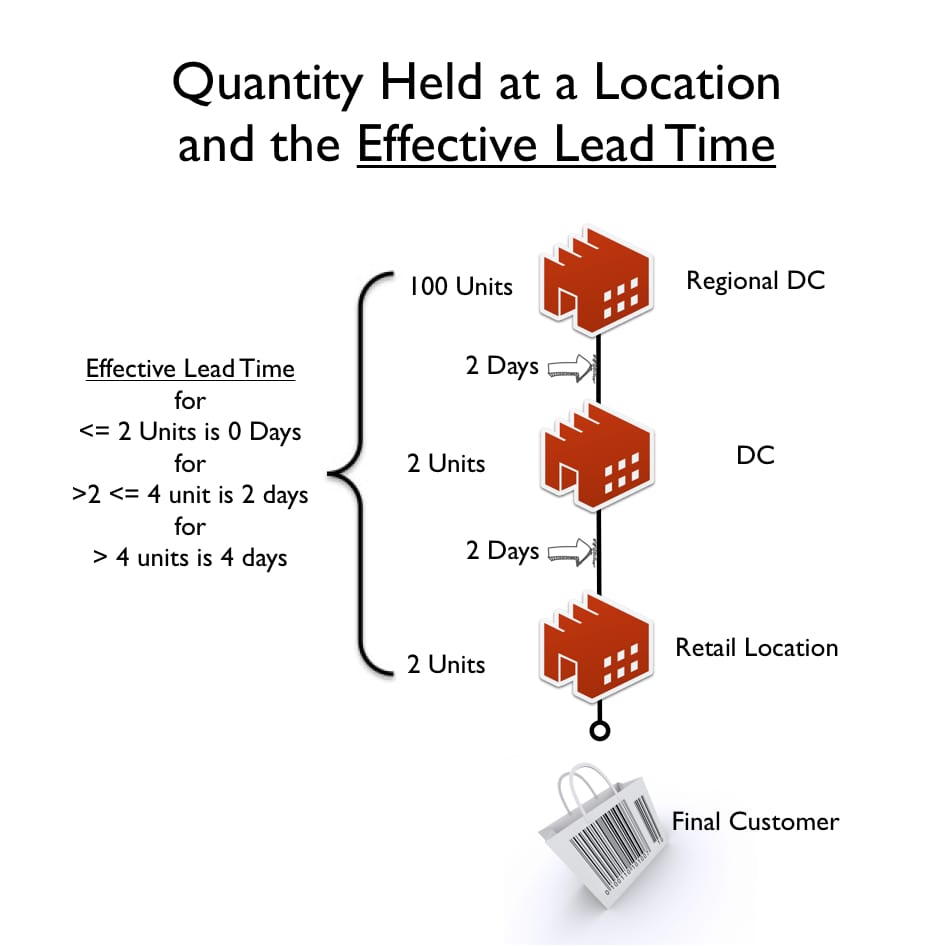
Other Users of the Term Effective Lead Time
Another use of the term is when a company needs to determine if it has the raw materials/components/packaging material to order quantity. If a company can produce the sales order quantity from all input materials’ safety stock, then the effective lead time is the production lead time.
If the order quantity exceeds this, the effective lead time must include the procurement lead time.
This is covered in more detail in this article.
How Can One Use the Concept of Effective Lead Time?
Interestingly, the term “effective lead time “is unique to a particular class of supply planning software but is still helpful to understand as a concept even if that software category is not used.
Effective lead-time is the total lead-time required to deliver the product to its final destination. It is variable and dependent upon the stocking positions of higher echelons in the supply network. This is a conditional concept of lead time. A conditional concept of time for lead time is entirely foreign to the regular usage of the term lead time, which is static and hard-coded into a system.
When higher-level locations must be called upon to satisfy demand, this lengthens the lead time.
In the excellent paper by Cohen, Agrawal, and Agrawal on dynamic asset deployment, this is described below.
“Similarly, investing in additional safety stock at a central depot reduces the effective lead-time for replenishment at the “child” locations connected to it. This lead-time reduction will, in turn, affect the stocking requirements at the child locations. Alternatively, such decisions are often constrained by the budgets allocated to the service organization. Consequently, if a particular asset is assigned to a specific location, it affects what can be assigned to other locations. Thus, the service levels that can be offered to customers at various locations are affected by these decisions, and are, therefore, interrelated; a high level of service to one customer may imply a lower level of service to another.” – Achieving Breakthrough Service Delivery Through Dynamic Asset Deployment Strategies, Cohen, Agrawal and Agrawal 2004
Conclusion
The lead time is the time required to complete a supply chain process.
Lead times are one of the most important foundational components of supply chain planning. Many misunderstandings regarding business processes or supply chain planning systems have their source in a faulty understanding of lead times. An excellent example is that companies can switch to make-to-order manufacturing environments.
- Many people do not think of lead times as being, in fact, lead times.
- Lead times in most systems are static. However, some systems can be variable and dependent upon changing circumstances.
Lead times are any passing of time that can contribute to the time required to make something in the supply chain occur.
One of the most crucial lead time distinctions in companies is short lead-time items versus long lead time items. Most companies treat the planning of quick lead-time items quite differently from long lead time items.
What is often not included in cost calculations for moving to lower-cost items with long lead time items is the increased inventory costs and planning and updating costs incurred by accepting longer lead times.
Lead times, which change depending upon the circumstance of demand versus the inventory or planned inventory in the supply network, are called effective lead times. The only supply planning method that calculates effective lead times is classified as inventory optimization and multiechelon software.